For many years, high quality, long service and durability have been associated with austenitic stainless steels such as 304 and 316 grades that account for more than 60% of the Australasian market.
Popularity of these steels is due to a combination of good fabrication properties, reasonable level of corrosion resistance and satisfactory experience in many different applications.
Fluctuations in the nickel prices have led to an increased use of low-nickel alternatives that can be found among ferritic stainless steels, which essentially contains no nickel, or austenitic stainless steels in which part of the nickel content has been replaced by nitrogen stabilized in manganese, or lean duplex stainless steels with reduced nickel and/or molybdenum content. However, there has not been sufficient experience with application of these steel grades.
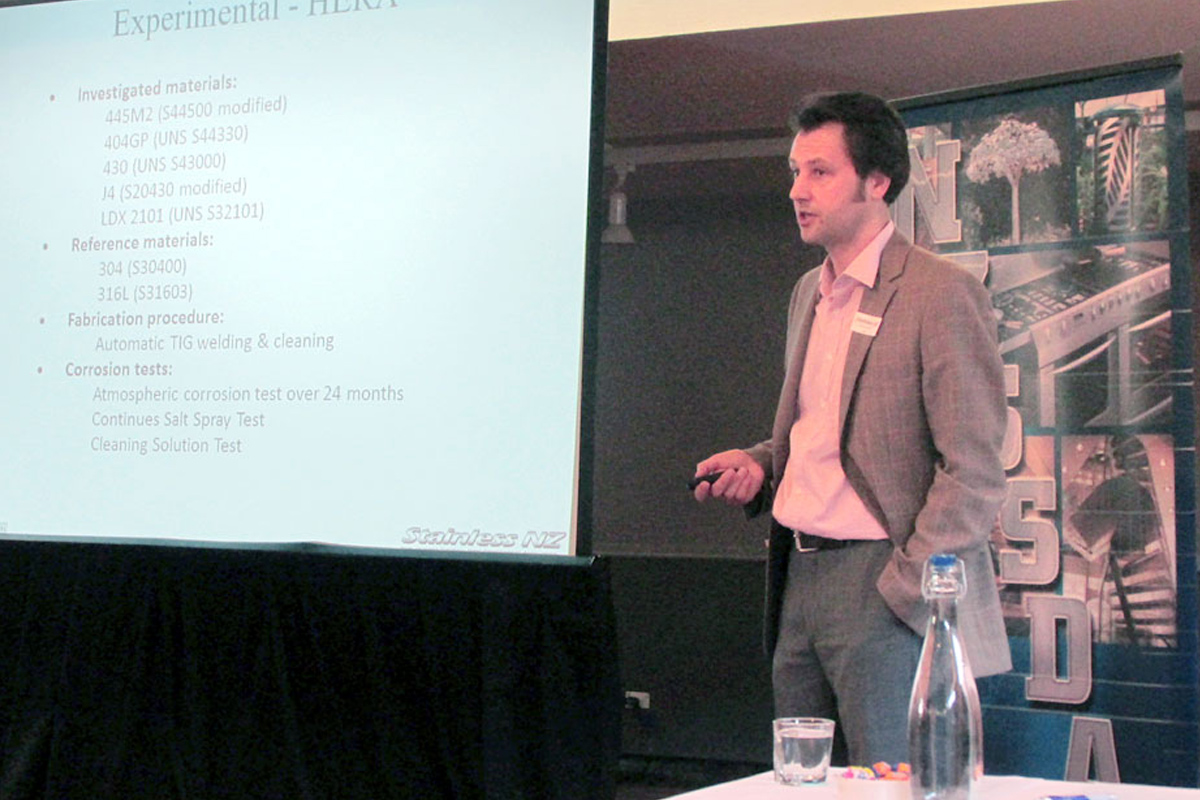
The majority of New Zealand stainless steel applications are located along the coastal line and therefore exposed to the marine environment. In this case, the grade selection is often governed by the need to prevent surface discoloration and corrosion from the sea salt spray.
HERA, in co-operation with NZ Stainless Steel Development Association (NZSSDA) and international partners University of Applied Sciences, Konstanz and BAM Bundesanstalt für Materialforschung und -prüfung Berlin, Germany, carried out comparative investigations where in each case, one or several representatives of a material group were taken into account.
The material groups covered were: Lean duplex stainless steels (2101, 2202 and 2304), manganese alloyed austenitic (J4, H400) and ferritic stainless steels (444, 445M2, 404GP, 441, and 3Cr12). Reference grades were 316 and 304.
The corrosion resistance in coastal atmosphere was tested at Muriwai Beach here in New Zealand and Helgoland Island in Germany. The same materials were tested over a period of 24 months. Specimens were taken from cold rolled and solution annealed plates with a thickness range from 1 to 2 mm.
The investigations were performed with specially worked surface conditions. The surface preparation included different methods, like grinding, polishing, welding and shot-peening. Figure 1 shows a test Rack that also includes coupons from New Zealand at the Island of Helgoland, Germany.
All materials showed some corrosion effects on the surface and the influence of the different surface conditions could be observed. Figure 2 shows an example of the kind of corrosion attack during exposure at the different locations. Besides the visual differences of the coupons, there are differences in the depth of the pits.
It can be observed that there are some differences in the corrosion resistance, depending on the test site, alloy composition and surface condition. It can be clearly observed that some of the stainless steels tested offer at least the same resistance as compared to grade 316.
Good resistance was observed in lean duplex stainless steels 2101 and 2304 and the molybdenum alloyed Ferritic Stainless Steels 444 and 445M2. These materials offer attractive corrosion properties compared to that of grade 316. However, when using ferritic materials the mechanical behaviour and weldability aspects must be taken into account.
Results of the corrosion tests were presented at the NZSSDA seminar on 15 October. They were also published in the papers referenced below. Further publications are being considered. A copy of the article can be obtained from our library.
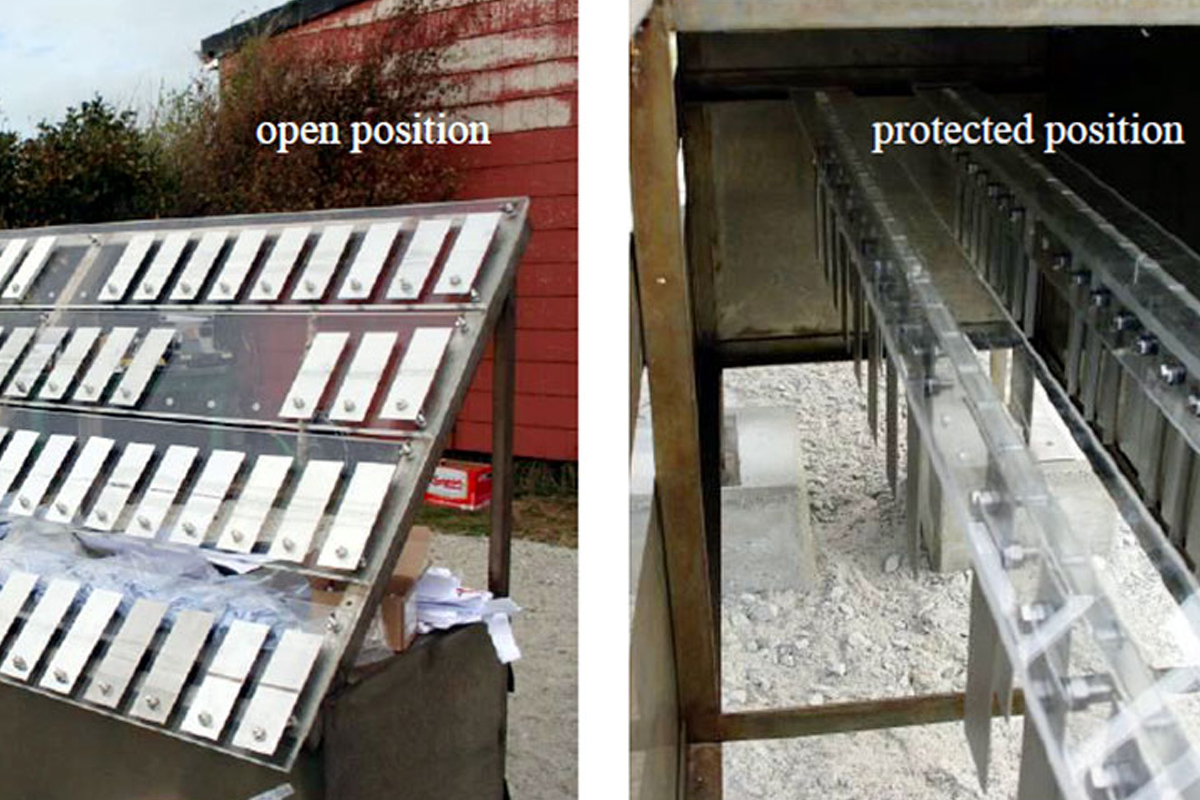
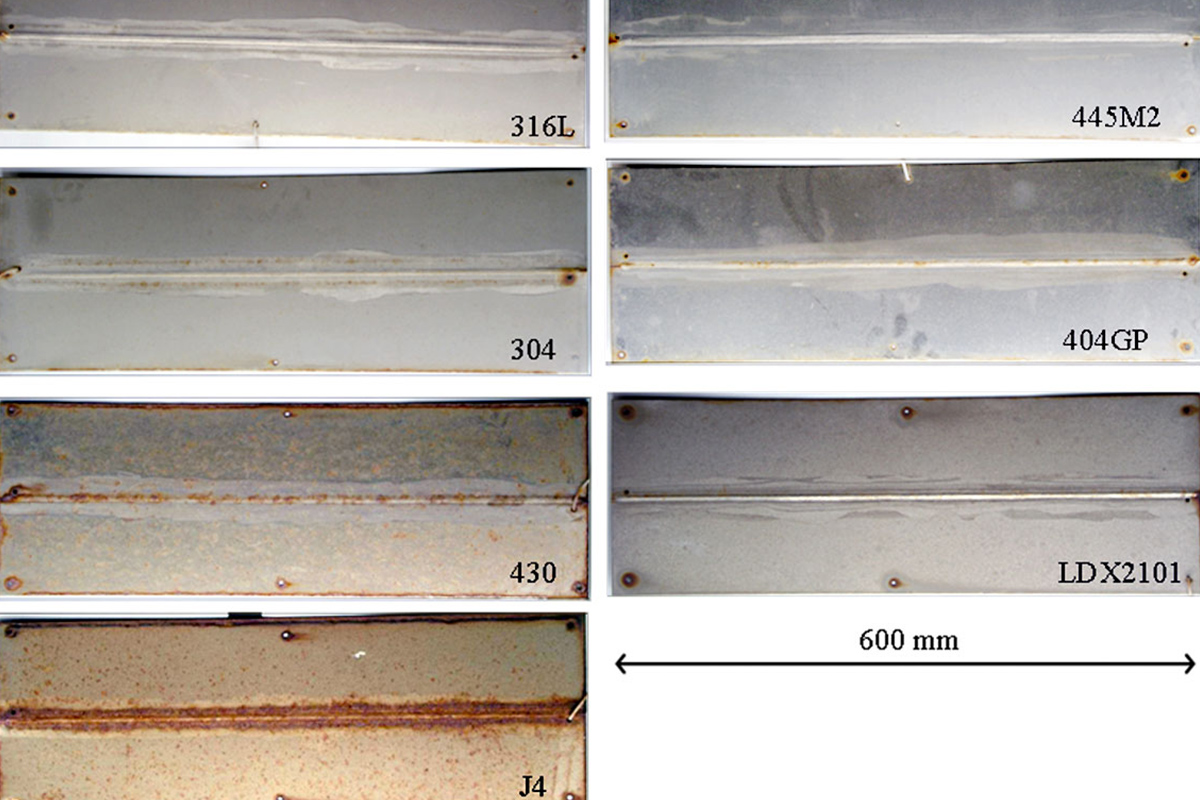
For more information you can also contact our General Manager Welding Centre Dr Michail Karpenko or Senior Welding Engineer Alan McClintock.
References
- Michail Karpenko, Paul Gümpel: Welding aspects and corrosion performance of new ferritic and manganese bearing stainless steels in the coastal environment. 18th International Corrosion Congress, Perth 2011.
- Paul Gümpel, Florian Leu, Andreas Burkert, Jens Lehmann and Michail Karpenko: Corrosion resistance of lean alloy alternatives for 300 series stainless steels – Part 1. Stainless Steel World, June 2014.
- Paul Gümpel, Florian Leu, Andreas Burkert, Jens Lehmann and Michail Karpenko: Corrosion resistance of lean alloy alternatives for 300 series stainless steels – Part 2. Stainless Steel World, July/August 2014.