Last month our Welding Research Engineer Holger Heinzel spent two weeks at the University of Wollongong (UoW) Facility for Intelligent Fabrication (FIF) gaining hands on experience on the latest technology. It’s valuable insight that we can’t wait to bring to our membership!
Whilst there Holger explored 3D scanning, virtual-reality assisted fabrication planning, CAD data driven tool-path generation, robotic cell setup, and 3D printing. It now means we’re well placed to carry out automation and productivity audits.
And, as part of our commitment to develop out this automation support, we’ll also be upgrading our own Welding Centre facilities to include robotic and industry 4.0 capabilities for research, demonstration and education purposes.
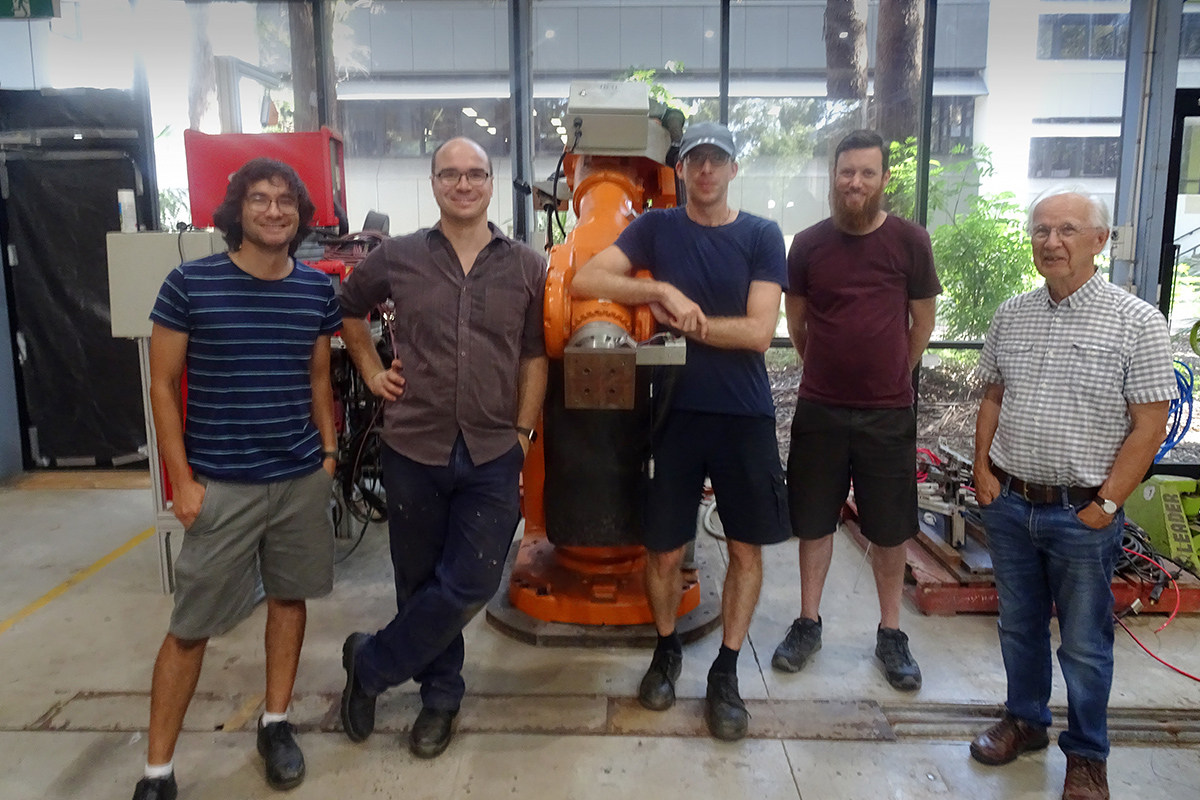
The UoW’s FIF is a technology transfer centre providing support and industry advice. Their core competences are in the area of welding and robotic automation. For over 30 years, they’ve been at the forefront of their field, carrying out research to develop new ways to integrate robots into the fabrication chain.
Being part of the university eco-system, the FIF’s research work is heavily supported by students, many of them at post-graduate level. The core team itself, consisting of highly enthusiastic people with a wealth of industry experience.
Programming and accuracy
The two main perceived challenges in robotic welding are programming time and the required accuracy of the setup.
A robotic arm for welding purposes usually has six degrees of freedom allowing a greater range of parts to be welded with optimum tool orientation. The addition of positioners or linear tracks can increase flexibility and increase the systems reach.
When it comes to programming, the multiple axes present a challenge to the programmer of the system. The tool of choice is often the touch pendant which is used to teach the robot where to go, point by point. A more elegant way is to use CAD data and a computer to generate the program for the robot.
Other systems also allow the robot to scan the work piece and identify possible weld locations itself. Based on this information, the user can select the seams on the screen, add weld data from a database and send the program to the robot. It’s a great tool for companies with ‘varying parts’ small production runs which otherwise wouldn’t be able to take advantage of the technology.
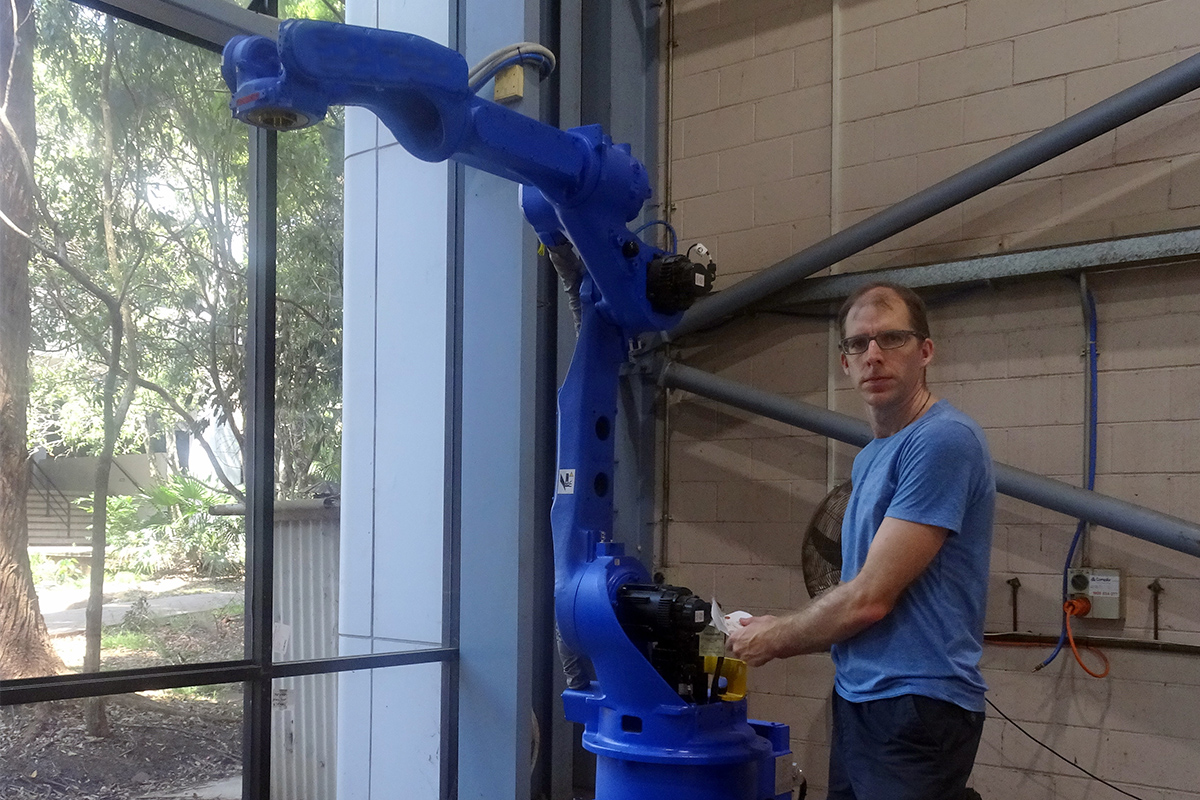
Traditional programming of a robot requires the parts to be located at precisely defined locations. The results are often expensive and complicated fixtures. Different technologies have been developed to alleviate this problem. Touch sensing is one of the lower-cost options to allow a robot to adjust its path based on the actual geometry of the part. More expensive systems use 2D or 3D visual sensors for this task. We’ll certainly be delving more into these technologies and will share our findings with you when we do!
Virtual Reality (VR)
Now that the program for the weld job on hand is generated, it’s time to verify that the robot is performing the required tasks. That is, that all the right bits are welded with the required settings and, of course, without damaging the part or the robot itself in the process!
Nowadays, it is possible to do all this without even leaving the office. A range of software packages are available to generate a digital replicate of the workshop setup and review the program. Throw on a pair of virtual reality glasses and the reviewing becomes truly immersive. This is also a great tool to communicate and discuss such programs with clients and customers.
Time to embrace the future
At HERA we know that automation of fabrication processes has been around for quite a while, and that our members are well aware of that. However, we’re equally aware that there is a perception that the associated cost and time for programming doesn’t make for a great business case. This is a perception we’re challenging.
While this may of been the case when it first came on our radar, today we can see newer developments are changing the equation. We urge our members to look again so they don’t miss the train.
That’s why, we’ll continue offering welding automation and productivity assessments to our members to identify fabricators and/or fabrication processes that they can automate. And, as mentioned, we’re also planning to have a facility set up for robotic and industry 4.0 capabilities such as VR so we can demonstrate it’s value first hand.
If you’re interested to learn more and explore this idea further for your business, join our Automation Innovation Cluster. This cluster allows us to coordinate services for like-minded members – developing productivity assessment programs for fabricators, exclusive opportunities, sharing of insights and more. Simply contact our Welding Research Engineer Holger Heinzel to become an active member!