Hot dip galvanizing is a process that involves immersing steel structures or components in molten zinc to provide a protective coating.
It is a crucial corrosion protection method for steel structures because it provides robust corrosion protection, extends the lifespan of the steel, reduces maintenance requirements, and offers numerous environmental and economic benefits. If executed correctly, hot dip galvanizing does not affect the properties of the galvanised steel. There are several standards and guidelines referenced below that should be considered.
In this article, we will have a look at the specific relationship between cold bending of steel and hot-dip galvanizing, shedding light on how this can impact the structural integrity of the component. During the hot dip galvanizing process, various factors can contribute to embrittlement and cracking in structural steels.
One of the primary issues is strain-age embrittlement, arising from the interplay between cold working processes, such as bending and shearing, and the subsequent heat exposure during galvanization.
Unveiling the Mechanism: Explore how strain-age embrittlement, combined with liquid metal-assisted cracking, lies at the core of the failure mechanism. The key indications of this phenomenon are fractures occurring at areas of cold forming, visible traces of zinc coating on fracture surfaces, and fractures primarily exhibiting an intergranular pattern. (see Figure 1 and Figure 2)
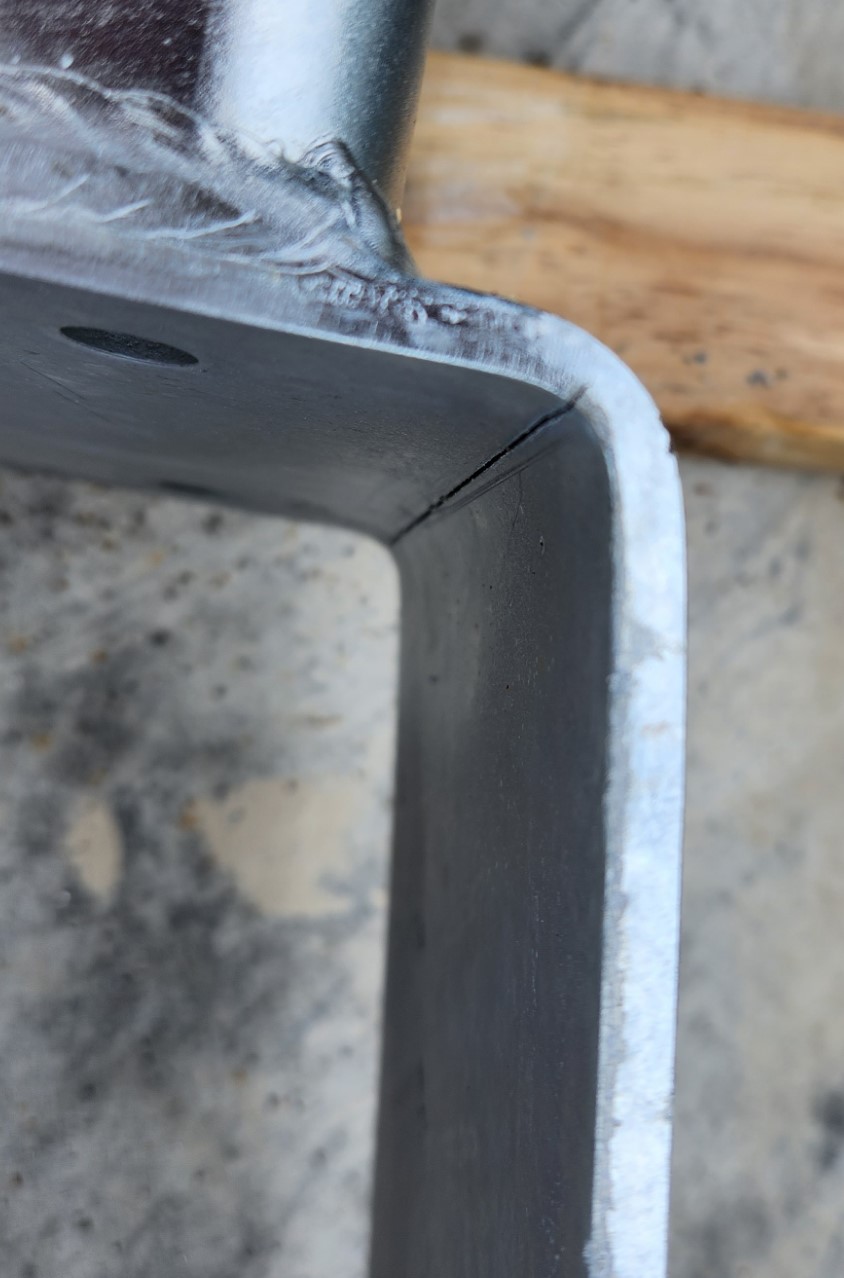
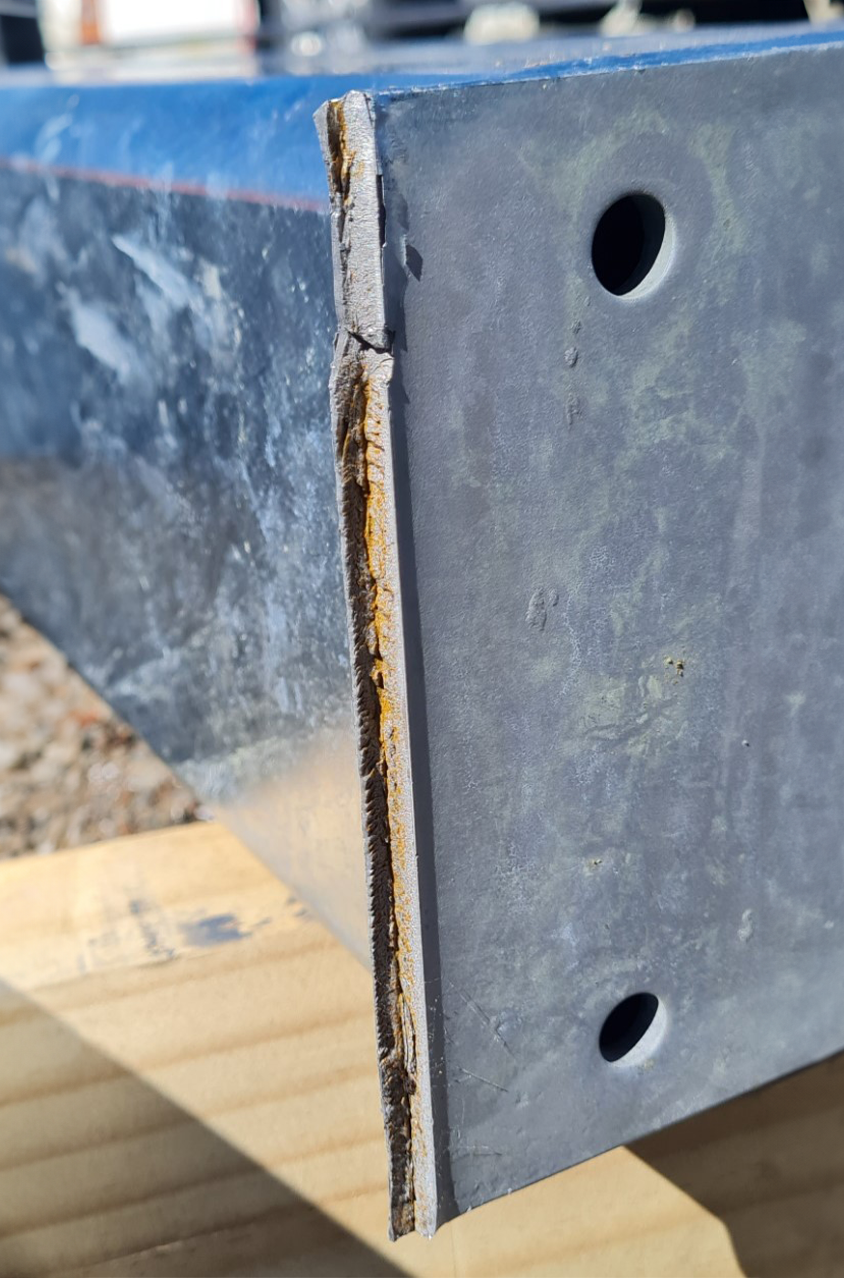
Strategies for Prevention: Bending to a suitable radius related to the material grade is typically the most economical option. Alternatively, hot forming can be used instead of cold forming. It can substantially mitigate the risk of cracking. Heat treatment prior to galvanizing can also be used to reduce the effect of cold bending if required. Guidelines such as those laid out in ASTM A143 come to the fore, with recommendations like maintaining a cold bending radius of three times the section thickness and employing post-cold bending annealing or stress relief techniques.
Smoothness Matters: The reduction in embrittlement risk can also be achieved through smoother inner bend corners offer valuable insights. Whether it’s adhering to specified radii or grinding flame-cut surfaces to achieve a seamless finish, the role of surface texture is crucial.
Navigating Standards and Guidelines: There are a number or resources available such as the Galvanizers Association of Australia’s Basic Design Guidelines, publications from the American Galvanizers Association (AGA), and standards like AS/NZS 4680:2016 to gain comprehensive insights into safeguarding against embrittlement during hot-dip galvanizing.
Engineering Excellence: The execution standard AS/NZS 5131, requires adherence to material standards for minimum radii during cold bending (Cl. 6.6.4 cold forming) and to thickness limitations for shearing of steel (Cl. 6.5.1). Recommendation for the minimum bent radii applicable to the steel grades can be also found in the following materials standards:
AS/NZS 3678:2016 Table C1, Recommended Minimum Inside Radius for Cold-Bending of Mechanically Tested Plate During Fabrication
AS/NZS 3679.1:2016 Table C1, Recommended Minimum Former Diameter for Cold-Bending of Rounds During Fabrication and Table C2, Recommended Minimum Former Diameter for Cold-Bending of Flats and Squares During Fabrication
AS/NZS 1594:2002 Appendix C, Recommended Minimum Internal Radii of Cold Bends in Forming
In summary, hot dip galvanising is a vital process to protect steel structures and components form corrosion. The galvanising process and the preparation of steel including bend radii shall comply with the applicable standards and guidelines to avoid potential issues with cracking in cold-bend areas. Recommendations for the minimum bent radii for different steel grades and thickness can be found in the materials standards above. Further references are included below.