As crucial as it is to be able to identify problems experienced by engineers – solving those problems with the right tools is equally important.
That’s because the element of uncertainty is there for the first part of the process, and for engineers – these problems are closely tied with design.
Today, virtual design and modelling is becoming common place and one almost expects it to be a given part of any process – but is that really true?
We’ve found that there are barriers stopping our metals-based industry from adopting tools such as Finite Element Analysis (FEA) into their workflow. The question is why?
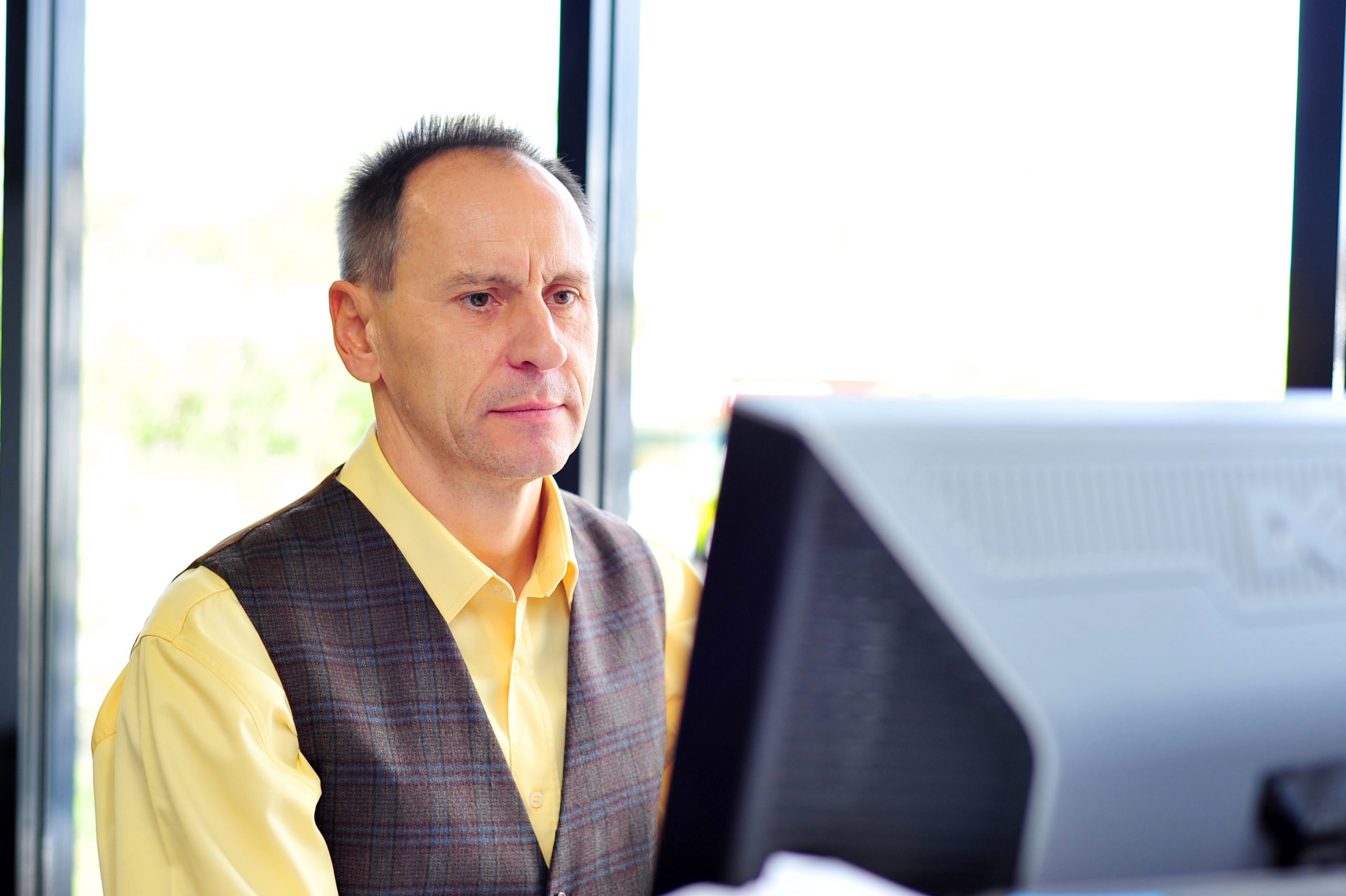
Eliminating uncertainty
Engineers are often concerned with creating new products that don’t exist and have never been done before. A challenge that often places the principle of uncertainty into their works.
There are several tools available to help eliminate or minimise such uncertainty in the design process. Among them are software such as 3D modelling and analytical tools. Typically, these can be applied to tackle a wide range of problems from mechanics, to heat transfer, floor vibration, fire performance and more.
In the case where the geometry and physics are sufficiently simple we’re able to yield accurate results. However, in reality – industrial products and processes are highly complex. As a result, simple physical relations are quickly replaced by complex partial differential equations and complicated geometries. Many resort to experimental testing of prototypes to close the knowledge gap – requiring significant investment of time and resources, which don’t always yield the certainty wanted.
At HERA, we’ve found that certainty of outcome is where FEA offers a main advantage. This is because it delivers a more detailed set of results that can offer the same, if not more certainty as traditional models and processes. Think of it like virtual 3D prototyping and testing, without the cost and time needed to manufacture those same prototypes.
Advantages of FEA include:
- Comprehensive result sets, generating the physical response of the system at any location, including some which might have been neglected in an analytical approach.
- Safe simulation of potentially dangerous, destructive or impractical load conditions and failure modes.
- Optimal use of a model. Often, several failure modes or physical events can be tested within a common model.
- The simultaneous calculation and visual representation of a wide variety of physical parameters such as stress or temperature, enabling the designer to rapidly analyse performance and possible modifications.
- Extrapolation of existing experimental results via parametric analyses of validated models.
- Relatively low investment and rapid calculation time for most applications.
Making a difference in project outcomes
We feel so confident in the benefits that FEA can deliver to our member’s projects that we’ve built up strong in-house capability in this service offering. Our Finite Element Analyst Nandor Mago lives and breathes FEA – bringing over 20 years’ experience working in this space.
As one of the country’s leading analysts, he’s able to help clients push their design boundaries when it comes to finding innovative solutions and de-risking the need for more costly and conservative design approaches.
Working on projects both nationally and abroad, he’s helped our member Beca Group by providing timely and critical support on their major multi-storey steel-framed building in Singapore. Giving them the confidence in their structural design to meet safety thresholds – in particular with the installation of tuned mass dampers to reduce floor vibrations.
He’s also delivered critical numerical predictions to estimate the fire performance of a composite slab with a re-entrant profiled steel sheet. Predictions that were subsequently verified through full-scale loaded fire tests conducted in the UK to obtain a fire rating to international standards. This work also led to the optimisation of the composite slab by eliminating the need for unnecessary reinforcement bars – a move that translated to $180K in cost savings to our client.
Your projects don’t have to cost the earth
The biggest risks are the ones you can’t see – which is why we believe adopting FEA should be the norm… not the exception when it comes to projects with uncertainty attached to them.
This is a message we particularly want our architects, structural engineers, design and build fabricators or others involved in the early design phase of a project to know.
We recognise there’s a perception that this work can be too costly, or time consuming – or only needed when a ‘big problem’ you can’t solve pops up. What we’d encourage you to consider, is that this work is an investment which in the long term improves the quality of an asset over its lifetime and minimises the risk for costly re-work. It also has the potential to significantly reduce costs by optimising designs.
Contact us today!
We’d like to invite those currently working on projects that may need FEA to contact our Finite Element Analyst Nandor Mago for a no obligation discussion on how we can help.
Software has come a long way and you’d be surprised at the advancements that have been made with the Abaqus software we utilise.
We’re so confident in our offerings that we’re also open to adopting different payment models that may be more suitable to the project at hand.