Have you introduced robotics into your business to improve productivity? HERA has an opportunity to help you enhance this offering!
Spot welding of car bodies was the first welding operation performed by automated robots in a production scenario. That was back in 1962, some 58 years ago.
Since then, robots have become commonplace in the manufacturing of school chairs, washing machines, rubbish skips, and ships to name just a few. All these items are produced at a large scale with only minor differences between them.
So, what about heavy fabrication? Products differ all the time and welds can be quite large. The critical factor is the time and skill it takes to programme a robot to the accuracy required to achieve a good quality weld.
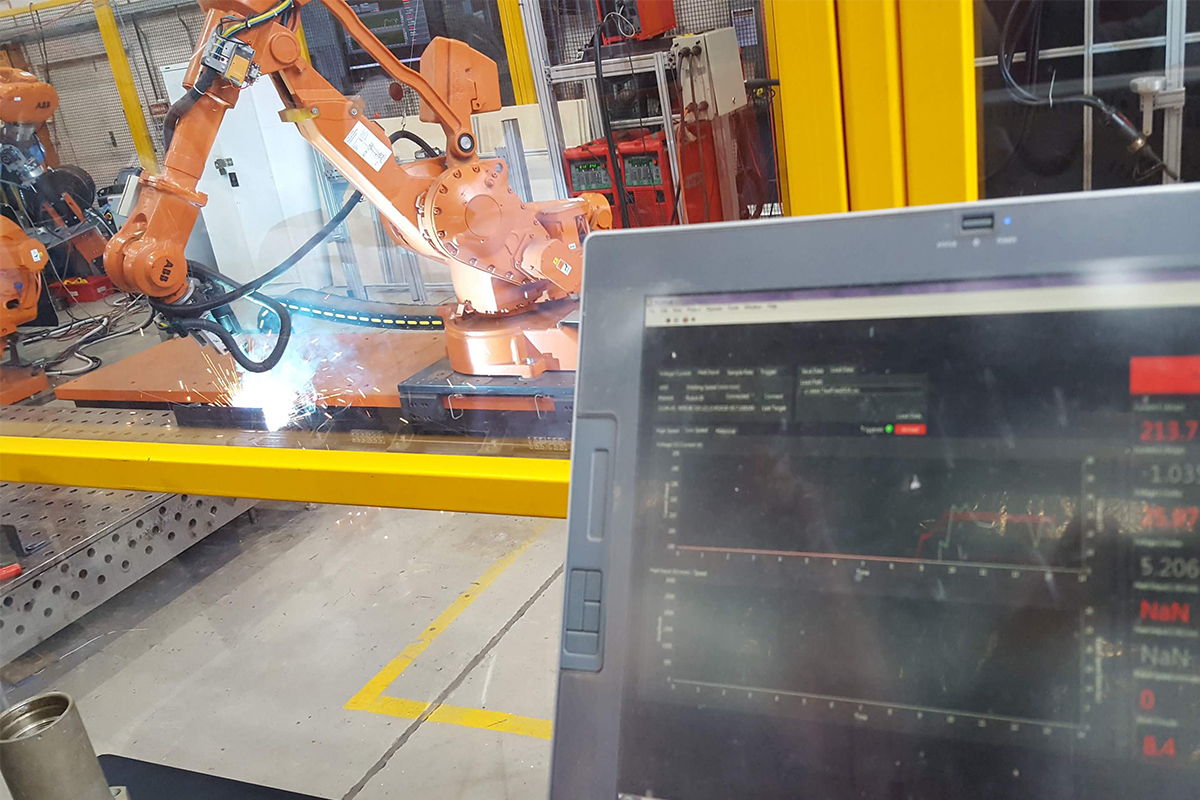
Times have changed!
Recent development in robot technology have much simplified the programming. Robots equipped with sensors can adjust the programming when parts are out of position and when weld seems move during welding.
Programming, at the same time, has moved away from the traditional step-by step approach using teach pendants. It is now carried out much faster and automated via computers or alternatively using co–operative robotics (cobots).
In the former approach, robot movements are created by a computer which is fed with a 3D model of the parts to be welded, while the latter uses the ability of a cobot to be programmed by manually moving the welding torch to the required location.
How can HERA help in your robotics exploration?
HERA has a long-standing relationship with the University of Wollongong (UoW) – one of the leaders in welding automation research. In particular, with Professors Emeritus Chris Cook and John Norrish who have been essential in setting up UoW’s robot research facilities and their establishment of a strong industrial footing.
This included some of our members having a chance to visit the lab at Wollongong University where they were highly impressed and inspired by the technology on display.
In 2018, our Fabrication 4.0 team were also joined by John and Chris for the welding and productivity audits of our members. The audits came back with mixed results. Some of the participating companies were very innovative in this area, most were still to catch-on to the bandwagon of automation and use of digital technologies.
Through these links, we’ve able to offer a member a fully supported one year licence of one of their Verbotics Weld software packages.
Verbotics is a recent spin-off out of UoW’s research activities. They’ve only been trading less than two year, and already their software is used by companies around the globe to automate programming of welding robots.
This project is one of HERA’s Industry 4.0 activities. The digital revolution that has changed our personal lives in so many aspects already is now taking place in industry. A recent survey and workshop have shown that HERA members are starting to take this onboard.
Have robots? Register your interest today!
This is a unique chance for a member to extensively evaluate the software and experience faster programming of their existing robots in a production environment.
To uptake this opportunity, the successful company will need to meet the following criteria, as well as allow HERA to report on the outcome of the project as a case study.
Registry of interest must be placed by close of business, 5 March 2021. HERA will then select one company for this program at its sole discretion.
Company eligibility criteria
- You must be currently using a Yaskawa (Motoman), Fanuc, or ABB robot for arc welding applications.
- Your robot controller needs to feature a controller which is compatible with Verbotics software. To note, most controllers produced in the last 15 years are suitable, but will need to be confirmed based on the specific model.
- Accept Verbotics EULA.
- Permit HERA the use of data associated with this project for analysis and reporting purposes and industry demonstrations
- Be able to provide a model of workcell and robot tooling and fixturing.
- Have experience in programming the robot.
- Have an accurate 3D model of a candidate workpiece.